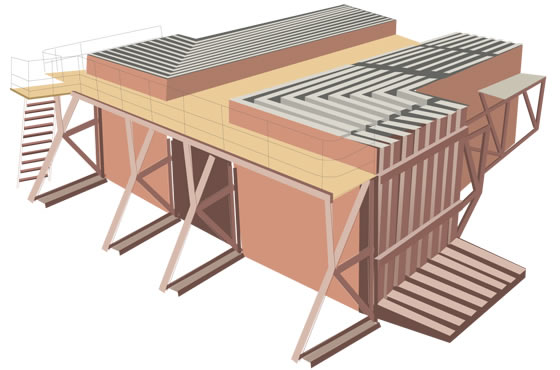
Battery Moulds
The patented steel battery moulds in which the panels are cast are capable of a very high rate of production and are equipped with hot oil pipework and sensors which enables two casting per day. A normal factory set-up will feature a four mould installation with each battery carrying 7 cells being sufficient to produce 56 panels in a 24 hour cycle. The sizes of the cells are adjustable to accommodate different leg lengths of the panels. The soffits to the moulds are also adjustable enabling different height panels to be cast. The cells are formed with steel leaves which open horizontally by a unique racking system to allow each cell to be set with fabric reinforcement and plastic conduiting and to be closed up when the mould is set and ready to receive concrete. Once one cell is set and ready for pouring, the next one can be opened and the process repeated. Once the complete battery is set, the main clamps are secured and the hydraulic rams activated. These devices ensure that there is no movement of the cells, end formers or soffits during deposition of the concrete and are essential to ensure the finished panel is cast within the very tight tolerances required.
The concrete used is dispensed from the batching plant and generally has a minimum cement content of 350kgs per cubic metre. This is to enable the concrete to have a high early strength sufficent to allow removing from the moulds after some 4 to 5 hours in conjunction with the hot oil curing. After approval from the Q.A. Manager, the moulds are opened and the concrete is tested to establish it’s strength whilst still in the cell and if it meets the strength requirement, de-moulding can take place. The panels are carefully removed from the moulds by the overhead gantry crane and deposited in the curing yard where it will remain for some 7 days in order to attain approximately 90% of its final strength being sufficient for it to be transported, fixed into position and loaded. After removal from the cells, the steel plate lining the cell is cleaned and sprayed with de-moulding oil ready for the next cast.