How it all works
The Elcon Battery Moulds
The vertical battery moulds comprise pairs of casting cells, typically 14 in a minimum two mould set – up. Most Elcon factories comprise a four mould battery which gives the capability of producing 28 ‘L’ shaped wall panels in a single day. all the cells have a system of curing pipework and with the addition of a thermal heater, two casts a day can be achieved, doubling the output. Each casting cell is adaptable which means that any ‘L’ shaped panel can be cast to any size up to 6m long (long leg), 2.5m (short leg) and up to 3m high.
As with any moulding process, it is essential that no deformation occurs in the mould during the casting process. The moulds are therefore a very robust structure made from structural steel sections and plating. Once the concrete is poured in the moulds, encapture bolts and tie rods are used to fasten the cells securely to each other and then the complete battery is pressurised with a series of hydraulic rams.
On reaching initial curing, the hydraulics and encapture systems are released, the leaves forming the casting cells are opened up and the formed ‘L’ shaped wall panel extracted by the gantry crane. The panels are then stacked and left to cure before transporting to site.

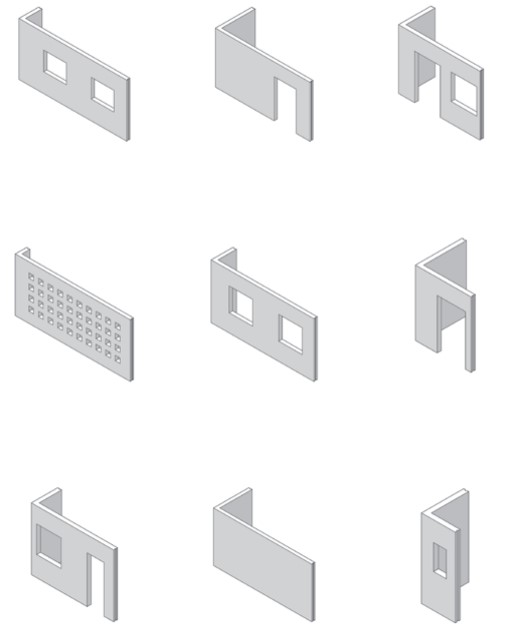
‘L’ shaped panel uses
The end product, being of high strength concrete, is generally used as a load bearing wall member of most types of building structures and many different types of flooring systems can be used with them. as the `L’ shaped panels have great strength, most structures using them do not need columns or beams. The system is ideal for compartment type structures in the form of housing, apartments, schools, hospitals, student accommodation and hotels, in fact anything with rooms up to 10m span. Elcon’s track record over the past 30 years provides an proof of the variety and flexibility of the system’s uses.

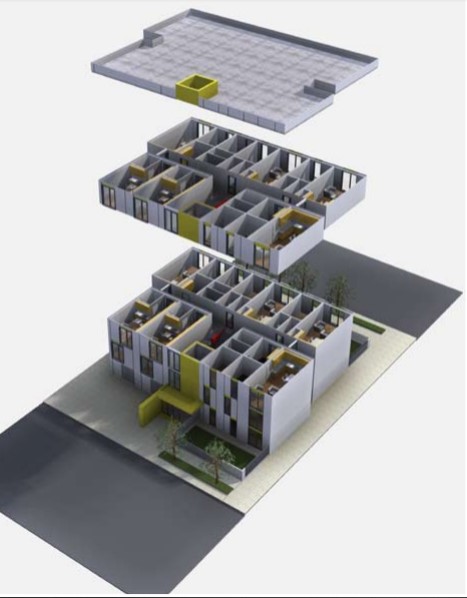